Gearing up to support the healthcare industry
Primo is gearing up to support its customers in a range of specialized industries. A Test & Innovation Centre has been established and new, dedicated test lines increase time-to-market and speed of innovation. Furthermore, a newly established team of material specialists is working closely together with the Medico team to investigate new and more sustainable materials.
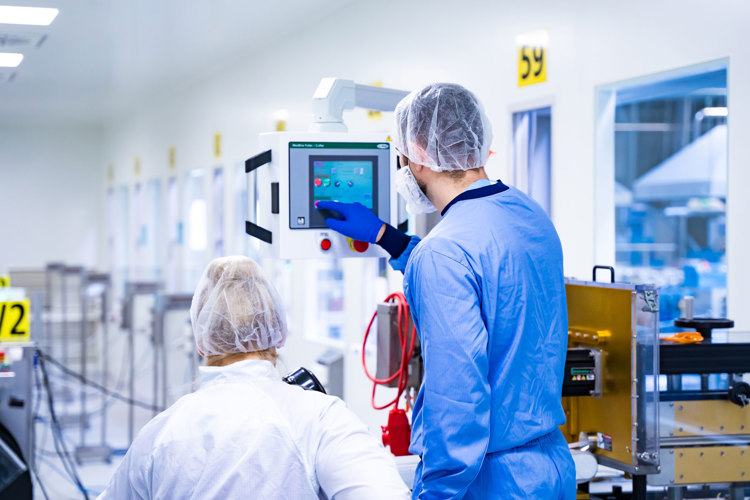
At Primo Medico, we have a specialised setup for developing new prototypes fast and efficiently. We can create new procedures and products with dedicated test lines; this is often difficult to do in a production setting. Furthermore, we have the knowledge and skills required for venturing into new products and materials and handling the ever-growing field of regulations.
Facilitating increased time-to-market
These situations occur more often in the industry. The pace of new products being tested is increasing. So is the establishment of new production facilities. The need for time-to-market while maintaining a high level of quality is also becoming more critical.
"We take pride in supporting the medical industry as a reliable extrusion partner who delivers quality on time. This also goes for complex manufacturing such as co- and tri-extrusion," says Daniel Kulwas, International Business Development Manager at Primo.
A flexible level of integration
Quality on time is made possible due to Primo's dedicated test lines for the medico-industry, a clean room for sterile manufacturing, and other adequate production facilities.
"These facilities allow us to work in-depth with our customers in the healthcare industry. We even take over some customers' in-house extrusion, sometimes using our customer's raw materials for extruding to ensure maximum alignment with the customer's production. The level of integration is flexible and completely dependent on the customer's need," says Tomasz Grzywaczewski, Director of the Medical Department at Primo.
Speed is not all
Primo’s medical section is installing high-speed production lines to support customers. But speed is not all, says Daniel Kulwas, International Business Development Manager at Primo.
"Speed is just one of more key features of our setup. For instance, post-production, such as packaging, cutting, and quality control, must follow the extrusion speed. Again, dedicated production lines come in handy. We can use more than one production line to setup up dual production in case of a demanding production with many secondary requirements."
Achieving better maneuverability
An excellent example of this is Primo's automated packaging which, in some cases, can reduce the customer's need for a workforce from six to only two.
"Flexibility is the main concern when working with the medical industry. When we provide increased delivery security, our customers will gain more maneuverability. This is important for developing new products, when relocating, managing regulations, and at peak production loads. At all these areas where the usual production at our customers is put to the test, we are there to assist," says Daniel Kulwas.
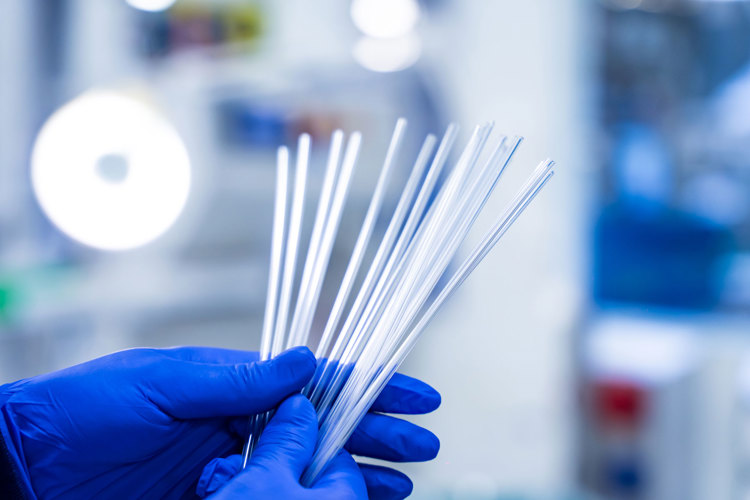
Primo at Compamed 22
Primo Medico is exhibiting at the coming Compamed, taking place 14-17 November. You can find us in hall 8A, booth no R11. We would very much like to share our specialist knowledge about medical tubing, extrusion and production processes and all the latest in polymer technology with you.
About Primo
Headquartered in Copenhagen, Denmark, Primo A/S operates 12 sales and production sites across Europe, China and the USA. Founded in 1959 by the Grunnet family, Primo specializes in custom-designed plastic profile solutions. The company employs around 1000 people and reported a turnover of 180 million EUR as of December 31, 2024.