In-depth material and process knowledge
To succeed in the lighting industry, producers must rely on dedicated partners and suppliers to research, develop and invest. Primo is investing heavily in research and development to meet the demands from the industry and support customers innovation with in-depth material and process knowledge.
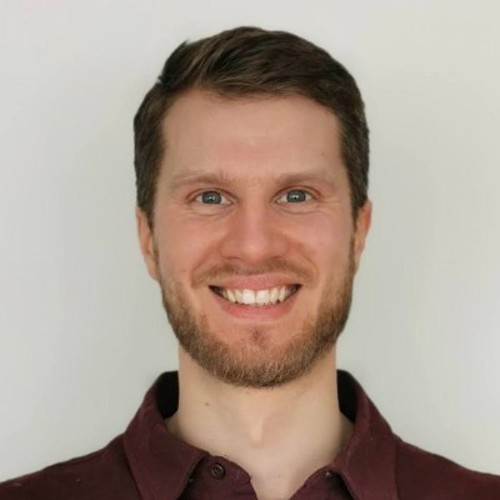
For decades, Primo has produced busbars for customers in the lighting industry. The development started together with Nokia, known as Nordic Aluminium today. The busbar production and useful contacts in the lighting industry gave Primo an advantage when the market for linear LED luminaries started to boom around 2010. Companies within the lighting industry today profit from Primo’s long and dedicated effort to identify the optimal raw materials and processing techniques. Primo’s targeted strategy focuses on the busbar and LED-industry, and recently Primo has invested in new production lines.
In-depth material and process knowledge
We are here for you all the way
"Concerning busbars, the major benefits of using extruded polymer profiles for lighting are insulation. Furthermore, the limited weight of plastics allows for lighter structure designs. Also, polymers such as acrylics (PMMA), have superior optical qualities that are better than glass, while polycarbonate (PC) has superior impact resistance and flammability values," explains Business Area Manager Jaakko Salo, Primo.
Another benefit is that it is possible to enhance raw material features such as UV-resistance, light diffusion, haze, chemical resistance – and even to combine different materials into a single profile that can substitute several components and fulfil multiple purposes.
"The extrusion of polymers is less energy demanding than the production of glass or aluminum, you will achieve a significantly lower CO2 footprint by using polymers over traditional raw materials," says Jaakko Salo.
Since the company implemented Lighting industry as part of the "Primo Drive" strategy, there have been several developments that enhance Primo's ability to supply significant players in the market with increasingly smart materials and products. Microprismatic and co-extruded solutions have been the "thing" on the market for a couple of years, but now Primo's customers are more often demanding solutions for controlling the light using linear lenses. Besides the functionality improvements, safety and environmental improvements are a major driver for development
"Together with our lighting track system customers, we have developed a halogen-free busbar, which is an alternative to PVC. We have been developing the manufacturing process for this solution for a number of years and successfully started up full-scale production ," says Jaakko Salo.
Developing efficient and economical solutions and following market trends is what Primo is all about. In the lighting industry, this is done in a close and open relationship with Primo's partners and customers.
Also, continuous investments in automatisation, such as packing machines and quality measurement devices, are essential in that process. Through automatisation, Primo secures competitiveness and products that fulfil all quality requirements.
"New solutions, applications and raw materials are continuously developed. We have to work closely together with our customers to help them reach their goals, but also to secure our competence proactively. We want to be part of the customer's development as early as possible and act in a "consultant role" from an extrusion standpoint. This way, the profile is optimised for production and, priority number one, meets all customer requirements," says Jaakko Salo.
Sustainability plays an important role in the plastic industry. Here Primo follows international best practices and invests in new technology to reduce waste.
"Sustainability is essential for us. Polymers are a sustainable solution due to low weight and recyclability. Furthermore, the production of extruded polymer profiles requires less energy due to low processing temperatures compared to glass, aluminum or steel. We are continuously developing solutions and processes to increase the reuse of our in-house scrap. To support this initiative, we utilize regrinding machinery for PC and PMMA. This enables reusing in-house scrap and reduces our total scrap percentage. We take part in "Operation Clean Sweep" and "Responsible Care Act" initiatives. These initiatives, in addition to recycling, commit us to design long-lasting products and to improve the health and safety of our employees, the community and the environment as a whole," Jaakko Salo says.
About Primo
Headquartered in Copenhagen, Denmark, Primo A/S operates 12 sales and production sites across Europe, China and the USA. Founded in 1959 by the Grunnet family, Primo specializes in custom-designed plastic profile solutions. The company employs around 1000 people and reported a turnover of 180 million EUR as of December 31, 2024.